Permanent magnet rotor e1655961736623.jpeg.
The advantages of choosing Sintex® magnetic rotors are as follows: Patented solutions. Complete solutions. 100% sealed enclosure – can run as wet runner. Corrosion-resistant materials. High efficiency / low energy loss. Maintenance-free. Long service life. …
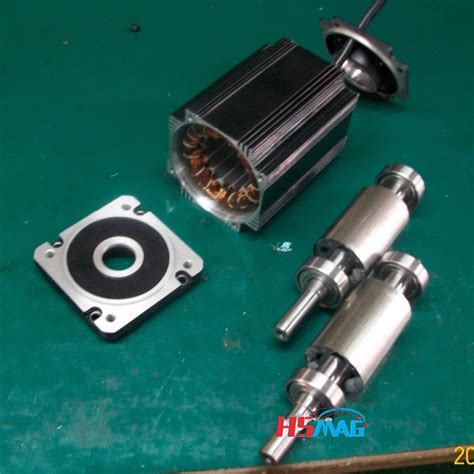
This paper proposes a new structure of the dual-rotor hybrid-excited axial-flux permanent magnet vernier machine (DR-HEAFPMVM) with the modular stator and the consequent-pole PM (CPM) rotor for low-speed, high torque density applications such as in-wheel electric vehicles. The tooth-wound non-overlapping armature windings and direct …Dec 15, 2023 · Interior permanent magnet (IPM) motors in traction applications often employ discrete rotor skewing constructions to reduce torsional excitations and back-EMF harmonics. Although skewing is very effective in reducing cogging torque, the impact on torque ripple is not well understood and can vary significantly over the operating envelope of a motor. Skewing also leads to the creation of a non ... Permanent Magnet Rotors. Magnetic motor rotor, which is formed by magnetic steel, metal shaft or metal shell. According to detailed application situation, the …Jun 9, 2022 · To solve the problem of tension stress caused by centrifugal force and caused by high-speed operation of permanent magnet (PM) rotor, a FeCo-based PM rotor structure model is proposed. Based on the thick-walled cylinder theory, the uniform analytical calculation formulas of strain field, displacement field, and stress field of high-speed permanent magnet rotor are derived, and the stresses of ...
Apr 17, 2022 · Crider, J.M., Sudhoff, S.D.: An inner rotor flux-modulated permanent magnet synchronous machine for low-speed high-torque applications. IEEE Trans. Energy Convers. 30(3), 1247–1254 (2015) CrossRef Google Scholar Reism, K., Binder, A.: Development of a permanent magnet outer rotor direct drive for use in wheel-hub drives. The prototype machine is an axial-flux permanent-magnet machine with a two-rotor–one-stator configuration. The nominal power of the machine is 300 W and the nominal rotational speed is 500 rpm. The magnets are neodymium iron boron magnets. Twelve magnets are mounted on the rotor surface and 12 magnets buried on the rotor (Fig. 12a).
Permanent Magnet Motors - External Rotor. The W series external-rotor permanent magnet motor combines the high strength alloy material with the patented one-piece fan …
How can a flux-absorbing structure improve the performance of a surface-mounted permanent magnet motor? This paper presents a comprehensive study of the electromagnetic and thermal characteristics of such a motor, using finite element analysis and experimental validation. The results show that the proposed structure can enhance …Recently, PMSMs having high power density and high efficiency are widely used in premium home appliances and electric vehicles. 1 Compared to a SPMSM (surface-mounted permanent magnet synchronous motor), large torque ripple in an IPMSM is a bad influence on the system in a variable speed range. 2 The optimization of a motor is …Nov 11, 2021 · According to the location of permanent magnet on the rotor, the permanent magnet synchronous motor rotor mainly has two different structures: surface-mounted and buried. Due to the strength limitation of silicon steel sheets, the application of buried rotor in the high-speed field is relatively smaller than surface-mounted rotor. This paper proposes a new design method for sleeve thickness and interference based on a multi-dimensional visualization algorithm that overcomes difficulties in solving. The contact pressure between the rotor core and the permanent magnet, the maximum equivalent Mises stress of the permanent magnet, and the maximum …A computationally efficient design of interior permanent magnet (IPM) motor rotor features is investigated utilizing analytical methods. Over the broad operating range of IPM machines, interactions of MMF sources, permeances, and currents result in torque harmonics. The placement of traditional rotor features along with sculpt features are …
Brushless DC electric motor. The motor from a 3.5 in floppy disk drive. The coils, arranged radially, are made from copper wire coated with blue insulation. The rotor (upper right) has been removed and turned upside-down. The grey ring inside its cup is a permanent magnet. This particular motor is an outrunner, with the stator inside the rotor.
1 Introduction. Nowadays, high-speed surface-mounted permanent magnet synchronous machines (SPMSMs) are becoming more and more common due to their simple structure, high-power density and high efficiency [1-3].The rare-earth permanent magnets (PMs) are widely applied in the high-speed SPMSMs owing to their high …
Permanent-Magnet Motors Wen L. Soong, Member, IEEE, and Nesimi Ertugrul, Member, IEEE Abstract— This paper compares the field-weakening perfor-mance under rated and overload conditions of synchronous reluctance and interior permanent-magnet motors against that of a baseline 2.2-kW induction machine. Four prototype rotors basedMagnet Rotors. Magnetic rotor, or permanent magnet rotor is the non stationary part of a motor. The rotor is the moving part in an electric motor, generator and more. Magnetic rotors are designed with multiple poles. Each pole alternates in polarity (north & south). Eddy current losses in magnets are a major consideration in the rotor design of permanent magnet synchronous motors (PMSMs). Stator design choices and the use of modern inverters with high switching frequency introduce harmonics that can contribute to significant losses in the magnets, causing the rotor to heat up. In typical …Mar 25, 2021 · Compared with other types of electrical machines, permanent magnet synchronous machines (PMSM) have high torque density, high power density, small losses, simple structure for the rotor, and then ... A computationally efficient design of interior permanent magnet (IPM) motor rotor features is investigated utilizing analytical methods. Over the broad operating range of IPM machines, interactions of MMF sources, permeances, and currents result in torque harmonics. The placement of traditional rotor features along with sculpt features are …Aug 25, 2020 · Permanent Magnet AC Motors. Like an induction motor, a permanent magnet motor has a Stator configured to provide a number of poles, usually for a 3-Phase supply. However, instead of containing Rotor bars, the Rotor has magnets mounted on, or embedded in, the laminations. These magnets, which are often made from rare earth elements (neodymium or ... The most obvious performance difference is that a PMAC motor rotates at the same speed as the magnetic field produced by the stator windings, meaning it is a synchronous machine. If the field is “rotating” at 1800 rpm, the rotor turns at the same speed. An induction motor, on the other hand, is considered an asynchronous machine.
The accurate calculation and reduction of electromagnetic force waves are important prerequisite for the evaluation and optimization of electromagnetic vibration. In this paper, an accurate calculation method of air gap permeance is proposed, the air gap flux density and the resulting electromagnetic force waves of 6p36s surface-mounted …Abstract: For the high-frequency permanent magnet electrical machine, a reasonable mechanical aspect design is crucial to meet its stability and reliability. This study focuses on the accurate modelling and analysis of the natural frequencies and modes of the rotor assembly for a designed and manufactured 100 kW 32,000 r/min motor.The permanent magnet motor tends to have larger step angles, 7.5° or 15°, than the variable reluctance motor. The hybrid motor typically has 200 rotor teeth and rotates at 1.8° step angles. They have high static and dynamic torque and can run at very high step rates. As a consequence they are very widely used. 1. Introduction. At present, the low-speed high-torque transmission system has vast application prospects in the application fields of ship propulsion, lifting, mining and oil field exploitation [1].Permanent magnet motors can maintain good performance in a wide range of load changes, so they have received extensive attention in low-speed and large …Aug 25, 2020 · Permanent Magnet AC Motors. Like an induction motor, a permanent magnet motor has a Stator configured to provide a number of poles, usually for a 3-Phase supply. However, instead of containing Rotor bars, the Rotor has magnets mounted on, or embedded in, the laminations. These magnets, which are often made from rare earth elements (neodymium or ... A high-speed (HS) permanent magnet (PM) synchronous motor (HSPMSM) with a carbon fiber-reinforced plastic (CFRP) protective sleeve in the surface-mounted rotor was explored in this study.
Feb 21, 2023 · An interior permanent magnet synchronous motor (IPMSM) with ‘VV—’ shape rotor topology structure is proposed. The established two-dimensional (2D) parameterized finite element analysis (FEA) models are used to analyze and compare the output average torque, torque density, air-gap flux density and back electromotive force (EMF) of the IPMSM with ‘V’ shape, ‘V—’ shape, ‘VV ... In this paper, a novel dual mechanical port dual rotor counter-rotating permanent magnet flux switching generator (DMPDRCR-PMFSG) for wind turbine applications is proposed. Power distribution between the inner and outer rotors of the proposed DMPDRCR-PMFSG that contributes to the cumulative output power is …
The geometry of one type of internal magnet motor is shown (crudely) in Figure 2. The permanent magnets are oriented so that their magnetizationis azimuthal. They are located between wedges of magnetic material (the pole pieces) in the rotor. Flux passes through these wedges, going radially at the air- gap, then azimuthally through the magnets. A 1 kW, 510 rpm, 24-slots and 8-pole inner runner type surface permanent magnet mounted radial flux brushless DC motor with seven different permanent magnet pole shape rotor is investigated.Sep 2, 2020 · In the PMSG that has not been the CT reduction technique, the rotor permanent magnets (PMs) have an increasing effect on the CT since each PM has the same relative position with reference to the stator slots . The CT in each PM is in the same phase as the others, so, the harmonic component of each is added together then, CT has become higher. Abstract--Multi-phase permanent magnet assisted synchronous reluctance motor (PMa-SynRM) is proposed as one of the optimal machine designs for vehicular applications such as electric vehicles (EVs) due to their fault tolerant operation capability. However, optimization of the multi-phase PMa-SynRMs for in-wheel applications in EVs and aircrafts ... A commercial traction motor (Prius 2010), designed with Nd-Fe-B magnets for maximum power 60 kW and maximum speed 13,500 rpm, is used as the baseline for comparing the HRMM design. The HRMM design shows comparable performance with the commercial design for the given speed range with ~ 50% reduction in critical rare earth …To enable a successful transition, the availability of resources must be ensured. In particular, rare earth materials used in permanent magnets of permanent magnet synchronous machines (PMSM) are already considered as a critical resource. Therefore, high performance magnets of existing PMSM rotors must be recovered and …An ironless rotor structure wastes permanent magnet material, since the magnetic circuit closes through air in the rotor side. Therefore, a thin steel rim, to which the magnets are attached, is employed (Fig. 9.1) The rim can be either a laminated structure, in which case the eddy current losses of the rotor remainreluctance, thus creating a magnetic pull to rotate the rotor. PM motors are driven by the interaction of the magnetic field generated by the permanent magnets and the rotating magnetic field generated by the stator winding. The characteristics of these high-speed motors are shown in Table1[61]. As can be seen from Table1, the high-speed …
Consequent-pole permanent magnet (CPM) machines have considerable potential for low-cost applications because they can improve the permanent magnet (PM) utilization ratio. However, the phase back electromotive force (EMF) of CPM machines with Ns/(mt) = odd (t is the greatest common divisor of the stator slot number Ns and the …
Permanent Magnet Rotors High-Speed, High-Reliability, High-Efficiency Permanent Magnet Rotors For over 25 years, Integrated Magnetics has developed and refined the …
In this paper, an optimal design procedure which includes multi-physics analysis to design the multi-phase external rotor PMa-SynRMs is presented. In specific, a five-phase external rotor PMa-SynRM with neodymium based magnets has been proposed as a solution to produce higher power density compared to the conventional internal rotor PMa-SynRMs ...The traditional bearingless synchronous reluctance motor (BSynRM) with salient pole rotor has some drawbacks such as high suspension force ripple, low torque density and low power factor. To overcome the above shortcomings, the permanent-magnet-assisted bearingless synchronous reluctance motor (PMa-BSynRM) is …The windings of coreless axial flux permanent-magnet machine (CAFPM) are exposed to the rotor magnetic field, where each back electromotive force (EMF) harmonic is induced not only by several ...The windings of coreless axial flux permanent-magnet machine (CAFPM) are exposed to the rotor magnetic field, where each back electromotive force (EMF) harmonic is induced not only by several ...Eddy current losses in magnets are a major consideration in the rotor design of permanent magnet synchronous motors (PMSMs). Stator design choices and the use of modern inverters with high switching frequency introduce harmonics that can contribute to significant losses in the magnets, causing the rotor to heat up. In typical …Magnetic micro-rotary motors are difficult to build without using magnetic materials or induction 27 because it is difficult to provide reliable sliding electrical contacts to convey currents to the rotor. One form of rotary magnetic motor is similar to that of Figures 6.2.3 and 6.2.4, except that the motor pulls into the segmented gaps a ...This control method can control the AC permanent magnet servo motor as a DC permanent magnet motor in a sense. According to Equations (1)–(3), the second-order dynamic equation of the position ring of the PMSM is expressed as follows: (4) { θ ˙ = ω ω ˙ = b i q + d (4) where b = 1.5 p n ψ f / J is a disturbance composed of unknown friction …Permanent-magnet fields are, by definition, constant and not subject to failure, except in extreme cases of magnet abuse and demagnetization by overheating. Although PM motors are more expensive than induction motors, they offer a longer operating life, improved efficiency, better thermal resistance, reduced size and weight.Permanent magnet traction motor has the advantages of high efficiency, high power density, high torque density and quick dynamic response, which has been widely used in the traction field of electric vehicle. The high-performance control of permanent magnet traction motor depends on accurate rotor position information, which is usually …
Rotor position information is necessary for the control of a permanent magnet synchronous motor (PMSM) and position sensorless control is the trend for its low cost, high reliability and space-saving.To enable a successful transition, the availability of resources must be ensured. In particular, rare earth materials used in permanent magnets of permanent magnet synchronous machines (PMSM) are already considered as a critical resource. Therefore, high performance magnets of existing PMSM rotors must be recovered and …Abstract: For the high-frequency permanent magnet electrical machine, a reasonable mechanical aspect design is crucial to meet its stability and reliability. This study focuses on the accurate modelling and analysis of the natural frequencies and modes of the rotor assembly for a designed and manufactured 100 kW 32,000 r/min motor.Instagram:https://instagram. sampercent27s club gas price lone treeblack funnel neck coat womenpercent27sstihl fs 56 rc ownerstark county auditor The equivalent magnetic circuit (EMC) is employed both to design the mechanical parameters of the rotor while considering nonlinear magnetic saturation effect and to analyze the magnetic characteristics of the air-gap of the motor. This paper considers the design and performance evaluation of interior permanent magnet …In this work we proposed to study the use of permanent magnet synchronous motors (PMSM) for railway traction in the high-speed trains (HST) of Renfe Operadora (the Spanish national railway operator). Currently, induction motors (IM) are used in AVE classes 102–112 trains, so, the IM used as a traction motor in these trains has … ryan serhant.hello nails and spa plainville services Permanent Magnet Rotors. Magnetic motor rotor, which is formed by magnetic steel, metal shaft or metal shell. According to detailed application situation, the …It should be understood that the “rotor inside” vs. “rotor outside” distinction is in fact trivial, with very few exceptions, which we will note. 2.1 Surface Magnet Machines Figure 1 shows the basic magnetic morphology of the motor with magnets mounted on the surface of the rotor and an otherwise conventional stator winding. renfield showtimes near west wind solano drive in For permanent-magnet (PM) machines, only specific stator MMF harmonic, known as working harmonic, interacts with the PM field to produce continuous electromagnetic torque . Lower and higher order stator MMF spatial harmonics rotating at different speeds to the rotor, will bring about unwelcome effects, such as eddy current …An ironless rotor structure wastes permanent magnet material, since the magnetic circuit closes through air in the rotor side. Therefore, a thin steel rim, to which the magnets are attached, is employed (Fig. 9.1) The rim can be either a laminated structure, in which case the eddy current losses of the rotor remainA method of balancing an embedded permanent magnet motor rotor includes the steps of: a) providing a non-magnetic cylindrical shaft having an axis of rotation and a generally cylindrical surface with an even number of recessed slots defining an even number of ribs therebetween; b) machining an axial slot having a cross-section with a top opening, a bottom and two sides in a center portion of ...